I made this RAM you’ve never seen before - Micron Factory Tour (SPONSORED)
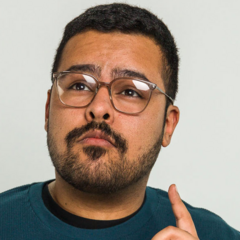
By
BellLMG
in LTT Releases
in LTT Releases
-
Featured Topics
-
Topics
-
1
-
superbrett2000 ·
Posted in Cases and Mods4 -
0
-
4
-
ItzTibby ·
Posted in Cases and Mods1 -
tanjackson ·
Posted in Storage Devices3 -
2
-
15
-
testcy ·
Posted in Power Supplies6 -
2
-
Create an account or sign in to comment
You need to be a member in order to leave a comment
Create an account
Sign up for a new account in our community. It's easy!
Register a new accountSign in
Already have an account? Sign in here.
Sign In Now